Micro geared motor consists of motor and gearbox, motor is the power source, motor speed is very high, torque is very small, motor rotational motion is transmitted to the gearbox through the motor teeth (including worm) mounted on the motor shaft, so the motor shaft is one of the very important parts in the micro geared motor.
I. Material of motor shaft
Shaft material selection should consider torque size, machinability, corrosion resistance, and whether to be magnetically conductive according to the motor requirements, the material can be selected from high quality carbon steel, stainless steel, alloy steel, carburized steel, etc. Commonly used motor shaft materials are the following types.
1. American Standard 1141 & 1144 steel, the closest domestic material is No. 45 steel, the most widely used material in the industry at present. The main disadvantage is that it is easy to rust, so when used, additional rust-proof oil needs to be applied to alleviate the problem of rusting.
2.American Standard 416 stainless steel, the closest domestic material is Y1Cr13. not easy to process, not suitable for processing with complex features, such as shaft head with threads, the price is more expensive than 45 steel, cheaper than 303, more widely used.
3.American Standard 420 stainless steel, the closest domestic material is 2Cr13. not easy to process, not suitable for processing with complex features, such as shaft head with thread, more expensive than 45 steel, cheaper than 416/303, more widely used.
4. American Standard 431 stainless steel, this material is not commonly used, mainly in contact with food occasions. Can be in contact with food.
5. American Standard 303 stainless steel, more expensive, characterized by soft material, easy to process into complex shapes.
II. The shape of the motor shaft
The motor teeth in the micro geared motor and the first level teeth in the gearbox mesh to transmit rotary motion, which will inevitably produce torque, so the fit tightness of the motor teeth and the motor shaft is very important. Consider the motor teeth and motor shaft fit, we can not get around the shape of the motor shaft.
Motor shaft shapes are
A. Light shaft, suitable for small load and small torque.
B. Flat shaft or D-shape shaft, suitable for medium load.
C. Knurled shaft, suitable for medium load.
D.Rotating shaft with keyway, suitable for heavy load and high torque.
E.The output end of motor shaft is worm, this kind of motor shaft is special, mostly used for turbo worm drive.

III. Process requirements of the motor shaft
Micro geared motors have life requirements, and the process requirements of the motor shaft also affect the life of the micro geared motor.
The processing technology of motor shaft has.
A.Motor shaft diameter size accuracy is relatively high, can be achieved within 0.002mm.
B. In order to prevent rust and improve corrosion resistance, the surface of the motor shaft is often electroplated with nickel.
C. The surface roughness of the motor shaft is also very important, which directly affects the precision of the fit with the motor teeth.
IV. Speed reducer drive shaft classification
The reducer is divided into high-power reducer and low-power reducer according to the power. The output shaft of various power, model and specification reducer is also different, and the transmission shaft of reducer is divided into output shaft and input shaft, and the principle of two kinds of shaft is introduced in detail below.
1. Output shaft
Output shaft is the shaft connected to the reducer and transmission mechanism, the output speed of the output shaft is much slower, according to the material output shaft is divided into metal output shaft, plastic output shaft; according to the shape is divided into customizable D-shaped shaft, round shaft, double flat shaft, hexagonal shaft, pentagonal shaft, square shaft, etc.
2. Input shaft
Input shaft is the connecting transmission shaft of transmission motor and reducer, input speed and torque of input shaft is small, shaft diameter; one end of input shaft can pass through the mounting hole and embed into the mounting cavity, input shaft can mesh with the gear in the mounting shell, mounting slot is opened at the other end of input shaft, then motor shaft of reducer motor is embedded in the mounting slot, and flat key is inserted between the flat key slot and motor shaft to realize the The fast and stable connection between the motor shaft and the input shaft is achieved. Through the above-mentioned cooperation between the input shaft, the mounting base, the mounting slot and the flat key slot, the geared motor can be quickly connected to the input shaft through the motor shaft, which facilitates the quick installation of the geared motor with the mounting housing and makes the loading and unloading of the staff more convenient.
3. The role and difference of the transmission shaft of the reducer.
A. transfer a certain amount of power.
B. Input speed rotation, output low speed rotation, to achieve the purpose of deceleration. In the premise of disregarding the friction resistance, the input shaft and the output shaft transfer equal power, and power = torque * speed, that is, when the power is equal, the torque and speed input shaft speed, so the torque is small, only a smaller shaft diameter; conversely, the output shaft speed is low, so the torque is large, must use a larger shaft diameter.
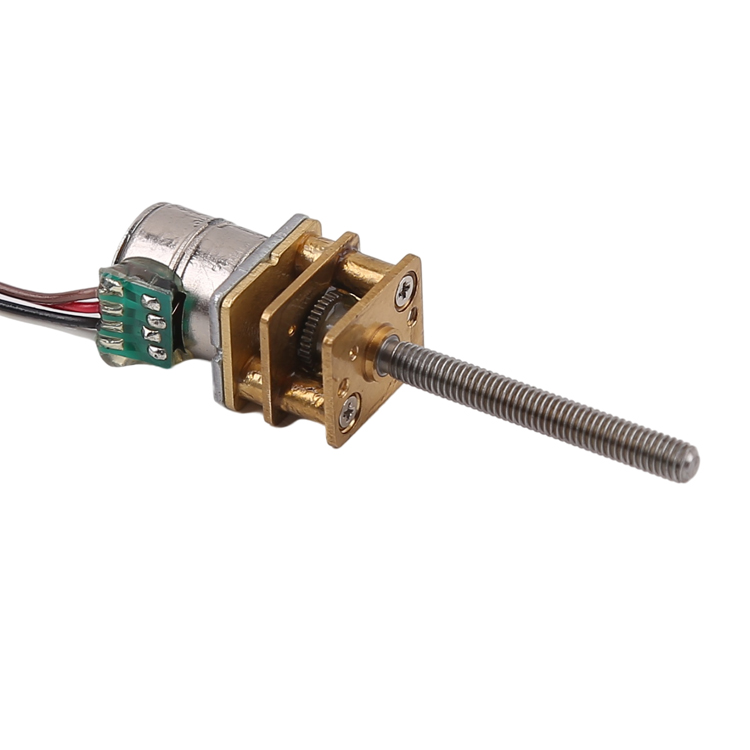
V. What are the reasons for the heating of the bearings of the miniature geared motor?
Micro geared motor in normal operation, the bearing will not appear abnormal heating, micro geared motor bearing heating serious usually have the following reasons.
1. miniature reducer motor bearing damage then will make the motor bearing overheating.
2. lubricating grease mixed with abnormal particles or foreign matter on the bearing will make the bearing wear increased overheating.
3. miniature reducer motor bearing oil shortage, if the motor in this state for a long time will make the friction increased resulting in bearing overheating.
4. the quality of lubricating oil is too poor, insufficient viscosity or too high viscosity, lubrication performance will also lead to abnormal heating of the bearing.
5. miniature reducer bearing and output shaft, end cover is too loose or too tight, too tight will lead to bearing deformation, too loose will lead to offset will make the bearing heating serious.
6. improper installation of bearings so that the two shafts are not in a straight line or bearing outer ring imbalance, then the bearing will not be sensitive, load running aggravated and heat.
VI. What are the basic reasons for axial runout of miniature motor?
1. The first case is the relative movement of the shaft and rotor of the micro motor, the rotor core and shaft with if for some reason the core hole and micro motor shaft core position clearance, which leads to the micro motor rotor core and shaft between the axial and radial relative position changes, there is a tampering shaft phenomenon, not only that, due to the axial movement of the rotor core, there is a high probability will lead to miniature motor end cap and rotor end friction deformation, or ripple to the stator winding.
2. the second case is the micro motor axial adjustment pad damage or leakage, we in the micro motor design and development process, the material thermal expansion factors are key considerations, so in the axial will leave a certain gap, but this will directly lead to axial displacement tampering axis, so the use of the method of loading the pad to solve, if the leakage of the pad or the quality of the pad is faulty, will lead to axial brake failure, tampering shaft.
3. The third case is the micro motor stator-rotor magnetic centerline automation alignment adjustment resulting in tampering, the ideal state of micro motor is the stator and rotor magnetic centerline completely overlapping, but in practice the micro motor stator-rotor is more difficult to achieve complete overlap alignment, so the micro motor in the process of operation will be out of this situation: "alignment - offset - alignment - offset Offset ------" so automatic alignment adjustment process, so repeated adjustment process will appear axial runout.
4. relative to the micro-motor with its own propeller in operation, the process of ventilation will produce a corresponding axial force on the micro-motor, if the propeller balance effect is not good, which will also lead to axial movement of the micro-motor.
Micro motor axial runout will produce the impact?
Simply put, if the miniature motor axial runout will make the miniature motor abnormal vibration, noise, bearing scattered, burned windings, reduce the service life of the situation. We can add waveform cushion to adjust the cushion on the outer edge of the miniature motor bearing and end cap nail to solve the problem of axial movement of the miniature motor.
VII. How to configure the bearings of the planetary reduction gearbox?
Planetary reducer configuration motor has been used in various fields such as smart home, so how is the bearing of micro reducer configured?
Generally micro planetary gearboxes use helical gears with a certain axial force, and even if double helical gears and spur gears are used, the axial direction must be positioned. The magnitude and direction of the meshing force of the gears can be determined, only the span of the bearing and the point of action of the force on the shaft are to be determined by drawing. Therefore, the following bearing selection can be made.
1, Common bearings are spherical roller bearings, single-row, double-row tapered roller bearings, double-row cylindrical roller bearings, four-point contact ball bearings, ball bearings, etc..
2, bearing specifications for the initial selection is to determine the shaft diameter bearing bore size, input shaft speed is higher, should be selected with the same bore in the larger load capacity specifications, the middle shaft has two pairs of gear meshing force acting on the bearing, in line with the larger, should also be selected with the same bore in the larger load capacity specifications;.
3, the output shaft speed is low and only a pair of gear meshing force acting on the shaft and bearing, you can choose the same bore in the load capacity of medium or smaller bearing, but the output shaft and the machine spindle rigid connection and impact, it should choose the bearing with greater load capacity.
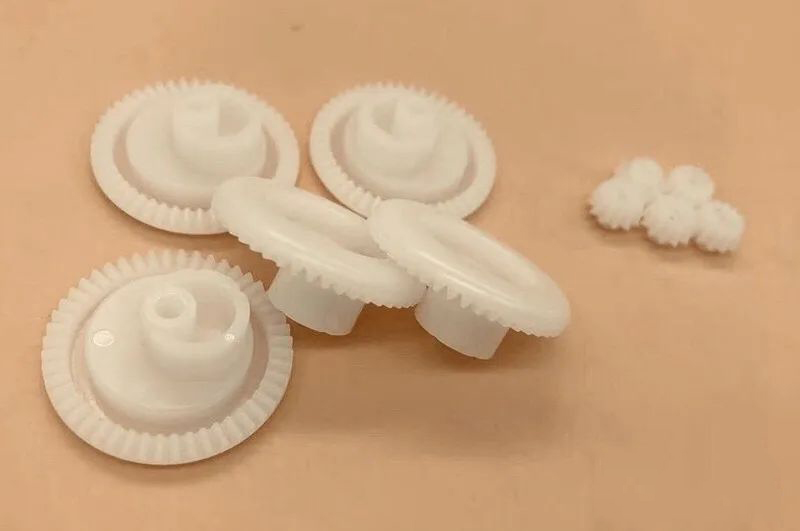
VIII. What will be the cause of a broken shaft in the gearbox of a gear motor?
In the daily work, in addition to the output of the reducer motor assembly concentricity is not good, and the resulting reducer broken shaft, the output shaft of the reducer if broken, no more than the following reasons.
First of all, the wrong type of selection leads to the reducer with insufficient force. Some users in the selection, mistakenly believe that as long as the selected reducer's rated output torque to meet the work requirements, in fact, it is not, because the rated output torque of the motor multiplied by the reduction ratio, the value of the belt in principle to be less than the rated output torque of similar reducers provided by the product samples.
Second, at the same time to consider the overload capacity of its drive motor and the actual large working torque required. In particular, some occasions must strictly comply with this guideline, which is not only the protection of the gears inside the reducer, but mainly the output shaft of the reducer is twisted off.
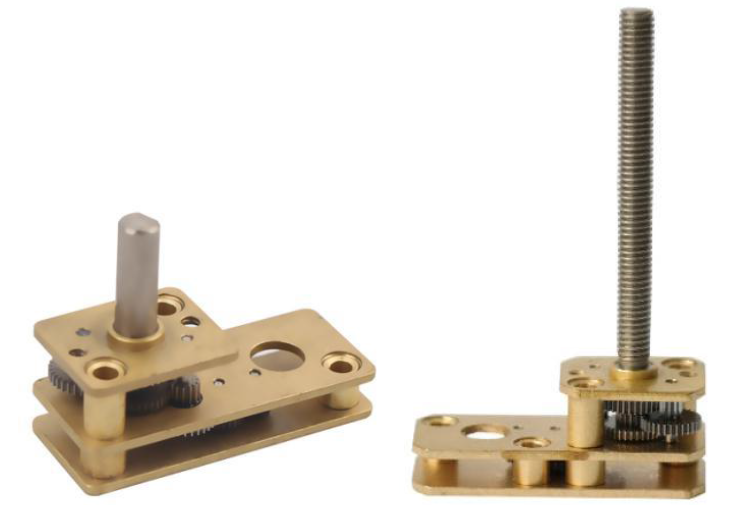
Post time: Nov-25-2022