Stepper motor is an open-loop control motor that converts electrical pulse signals into angular or linear displacements, and is the main actuating element in modern digital program control systems, which is widely used. The number of pulses can be controlled to control the angular displacement to achieve accurate positioning; at the same time, the pulse frequency can be controlled to control the speed and acceleration of motor rotation to achieve the purpose of speed regulation. Generally speaking, a common method to achieve accurate linear positioning is to connect the stepper motor and the sliding screw vice through a coupling with a guiding mechanism, which converts the rotary motion into linear motion through the engagement of threads and nuts.
The linear stepper motor uses unique advanced technology to integrate the screw sub and stepper motor into one unit, so that customers do not need to install couplings when using it, which not only saves installation space, but also can effectively improve the efficiency of system assembly. Linear stepper motors can be divided into four types according to the structure: external drive type, Non-captive type, fixed shaft type and slider linear motor
This article introduces the structural principle of Non-captive linear stepper motors and finally explains its application advantages.
The principle of Non-captive linear stepper motor
The Non-captive linear stepper motor integrates the nut and the motor rotor into one unit, with the screw shaft passing through the center of the motor rotor. In use, the filament rod is fixed and made anti-rotation, and when the motor is powered up and the rotor rotates, the motor will make linear motion along the filament rod. Conversely, if the motor is fixed and the filament rod does anti-rotation at the same time, then the filament rod will do linear motion.
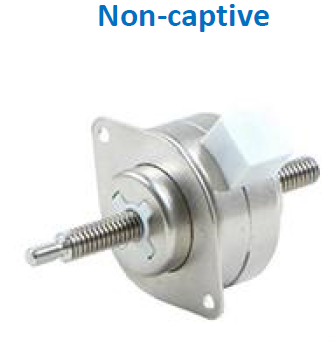
Application advantages of Non-captive linear stepper motors
In contrast to application scenarios where externally driven linear stepper motors are used with linear guides, Non-captive linear stepper motors have their own unique advantages, which are reflected in the following 3 areas.
Allows for greater system installation error.
Typically, if an externally driven linear stepper motor is used, there is a high risk of system stalling if the filament and guideway are not mounted parallel. However, with Non-captive linear stepper motors, this deadly problem can be greatly improved because of the structural characteristics of their design, which allow for greater system error.
Independent of the critical speed of the filament rod.
When an externally driven linear stepper motor is selected for high-speed linear motion, it is usually limited by the critical speed of the filament rod. However, with a Non-captive linear stepper motor, the filament bar is fixed and made anti-rotational, allowing the motor to drive the slider of the linear guide. Since the screw is stationary, it is not limited by the critical speed of the screw when achieving high speed.
Space saving installation.
Non-captive linear stepper motor, because of its nut built-in in the motor structure design, will not occupy additional space beyond the length of the screw. Multiple motors can be installed on the same screw, and the motors cannot "pass through" each other, but their movements are independent of each other. Therefore, it is the best choice for applications where space requirements are stringent.
Post time: Nov-16-2022