After the stepper motor starts there will be an inhibition of the rotation of the role of the working current, like the elevator hovering in mid-air state, it is this current, will cause the motor to heat up, this is a normal phenomenon.
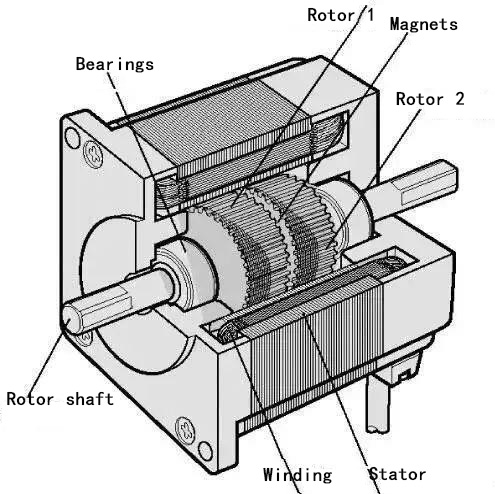
Reason one.
One of the most meaningful advantages of stepper motors is the precise control that can be achieved in an open-loop system. Open-loop control means that no feedback information about the (rotor) position is required.
This control avoids the use of expensive sensors and feedback devices like optical encoders, because only the input stepping pulses need to be tracked to know the position of the (rotor). Recently, some customers have reflected to our Shangshe motor engineers that stepper motors are also prone to heat problems, so how to solve this situation?
1, reduce stepper motor heat, reduce heat is to reduce copper loss and iron loss. Reduce copper loss in two directions, reduce the electric yin and current, which requires the selection of small resistance and rated current as small as possible when the motor, two-phase stepper motor, can be used in series motor not parallel motor, but this often contradicts the requirements of torque and high speed.
2, for the motor has been selected, should make full use of the drive's automatic half-current control function and offline function, the former automatically reduces the current when the motor is at rest, the latter simply cut off the current.
3, in addition, subdivision stepper motor drive due to the current waveform is close to sinusoidal, less harmonics, motor heating will be less. There are few ways to reduce iron loss, the voltage level is related to it, high voltage drive motor although it will bring an increase in high-speed characteristics, but also bring an increase in heat generation.
4, should choose the appropriate drive motor voltage level, taking into account the high band, smoothness and heat, noise and other indicators.
Reason two.
Stepper motor heat although generally does not affect the life of the motor, for most customers do not need to pay attention to. But seriously will bring some negative effects. Such as stepper motor internal thermal expansion coefficient of each part of the different structural stress changes and small changes in the internal air gap, will affect the dynamic response of the stepper motor, high-speed will be easy to lose step. Another example is that some occasions do not allow excessive heat generation of stepper motors, such as medical devices and high-precision test equipment. Therefore, the heat of the stepper motor should be necessary to control. The motor heat is caused by these aspects.
1, the current set by the driver is larger than the rated current of the motor
2, the speed of the motor is too fast
3, the motor itself has a large inertia and positioning torque, so even medium-speed operation will be hot, but does not affect the life of the motor. The demagnetization point of the motor in 130-200 ℃, so the motor in 70-90 ℃ is a normal phenomenon, as long as less than 130 ℃ is generally no problem, if you really feel overheated, the drive current is set to about 70% of the rated motor current or motor speed to reduce some.
Reason three.
Stepper motor as a digital actuating element, has been widely used in the motion control system. Many users and friends in the use of stepper motors, feel that the motor work with a large heat, have doubts, do not know whether this phenomenon is normal. In fact, heat is a common phenomenon of stepper motors, but what degree of heat is considered normal, and how to minimize the stepper motor heat?
The following we do some simple classification, hopefully in the actual work of practical applications:.
1 motor heating principle
We usually see all kinds of motors, the internal core and winding coil. The winding has resistance, energized will produce loss, the size of the loss and resistance and current squared proportional to the loss, which is often referred to as copper loss, if the current is not standard DC or sine wave, but also harmonic loss; core has hysteresis eddy current effect, in the alternating magnetic field will also produce loss, the size of the material, current, frequency, voltage, which is called iron loss. Copper loss and iron loss will be manifested in the form of heat, thus affecting the efficiency of the motor. Stepper motors generally pursue positioning accuracy and torque output, the efficiency is relatively low, the current is generally relatively large, and high harmonic components, the frequency of current alternation also varies with the speed, and thus stepper motors generally have heat, and the situation is more serious than the general AC motor.
2 stepper motor heat reasonable range
The extent to which motor heat generation is allowed depends largely on the motor's internal insulation level. The internal insulation will only be destroyed at high temperatures (above 130 degrees). So as long as the internal does not exceed 130 degrees, the motor will not damage the ring, and the surface temperature will be below 90 degrees at that point. Therefore, the stepper motor surface temperature in 70-80 degrees are normal. Simple temperature measurement method useful point thermometer, you can also roughly determine: with the hand can touch more than 1-2 seconds, not more than 60 degrees; with the hand can only touch, about 70-80 degrees; a few drops of water quickly vaporized, it is more than 90 degrees
3 stepper motor heating with speed change
When using constant current drive technology, the stepper motor at static and low speed, the current will remain constant to maintain constant torque output. When the speed is high to a certain degree, the motor's internal counter potential rises, the current will gradually drop, and the torque will also drop. Therefore, the heating condition due to copper loss will be speed dependent. Static and low speed generally generate high heat, while high speed generates low heat. But the iron loss (although a smaller proportion) changes are not the same, and the whole motor heat is the sum of the two, so the above is only the general situation.
4 heat brought about by the impact
Although the motor heat generally does not affect the life of the motor, the majority of customers do not need to pay attention to. But seriously will bring some negative impact. Such as the different coefficients of thermal expansion of the internal parts of the motor lead to changes in structural stress and small changes in the internal air gap, will affect the dynamic response of the motor, high-speed will be easy to lose pace. Another example is that some occasions do not allow the excessive heat of the motor, such as medical equipment and high-precision test equipment. Therefore, the heat generation of the motor should be controlled as necessary.
5 How to reduce the heat of the motor
Reduce heat generation, is to reduce copper loss and iron loss. Reduce copper loss in two directions, reduce resistance and current, which requires the selection of small resistance and rated current as small as possible when the motor, the two-phase motor, can use the motor in series without parallel motor. But this often contradicts the requirements of torque and high speed. For the selected motor, the drive's automatic half-current control function and offline function should be fully utilized, the former automatically reduces the current when the motor is at rest, and the latter simply cuts off the current. In addition, the subdivision drive, because the current waveform is close to sinusoidal, less harmonics, motor heating will also be less. There are few ways to reduce iron loss, and the voltage level is related to it. Although a motor driven by high voltage will bring an increase in high-speed characteristics, it also brings an increase in heat generation. So should choose the appropriate drive voltage level, taking into account the high speed, smoothness and heat, noise and other indicators.
For all kinds of stepper motors, the interior is composed of an iron core and a winding coil. The winding has resistance, energized will produce loss, the size of the loss is proportional to the square of the resistance and current, which is often referred to as copper meteor, if the current is not standard DC or sine wave, but also harmonic loss; core has hysteresis eddy current effect, in the alternating magnetic field will also produce loss, the size of the material, current, frequency, voltage, which is called iron loss. Copper loss and iron loss will be manifested in the form of heat, thus affecting the efficiency of the motor. Stepper motors generally pursue positioning accuracy and torque output, the efficiency is relatively low, the current is generally relatively large, and high harmonic components, the frequency of current alternation also varies with the speed, and thus stepper motors generally have heat, and the situation is more serious than the general AC motor.
Post time: Nov-16-2022